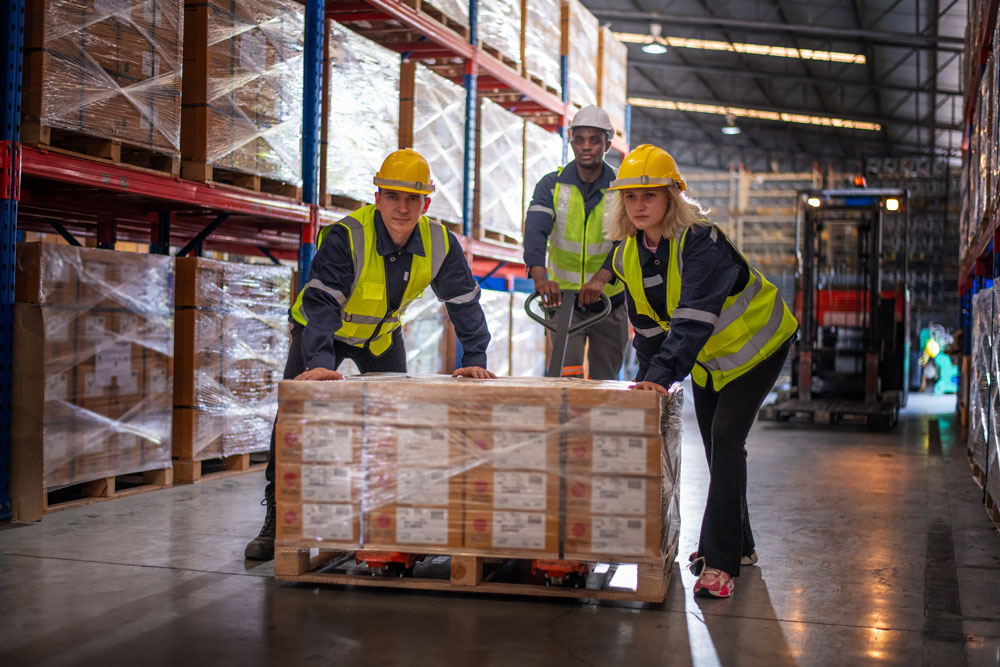
Running a retail business in the UK, whether you have a high street shop, an online store or both, means navigating a complex web of suppliers, manufacturers and logistics. In recent years, we’ve seen just how fragile these supply chains can be. From global pandemics to Brexit-related hurdles and even unexpected weather events, disruptions can have a significant impact on your ability to get products to your customers. This article will explore some of the key risks facing UK retail supply chains and, more importantly, outline strategies to build resilience and keep your business operating smoothly, whatever the challenge.
Understanding the Potential Threats
A robust risk management strategy starts with identifying the potential threats to your supply chain. For UK retailers, these can include:
- Geopolitical Instability and Trade Issues: Events like Brexit have already demonstrated the impact of changing trade agreements and border controls. Future political shifts or trade disputes can lead to tariffs, delays and increased costs for imported goods.
- Global Pandemics and Health Crises: As we’ve experienced, widespread health emergencies can disrupt manufacturing, transportation and even consumer demand.
- Supply Chain Partner Issues: The failure or instability of a key supplier, manufacturer or logistics provider can have a knock-on effect on your operations. This could be due to financial difficulties, production problems or even cyberattacks.
- Transportation Disruptions: Road closures, port congestion, strikes and fuel shortages can all delay the movement of goods, impacting both stock arriving at your physical store and online order fulfilment.
- Natural Disasters and Extreme Weather: Floods, storms and other extreme weather events can damage infrastructure, disrupt transportation and affect the availability of raw materials or finished goods.
- Cybersecurity Threats: Attacks on your own systems or those of your suppliers and logistics partners can disrupt operations, compromise data and damage your reputation.
- Labour Shortages: Shortages in key areas like HGV drivers, warehouse staff and port workers can lead to delays and increased costs.
- Fluctuations in Demand: Unexpected surges or drops in consumer demand, whether driven by trends or economic factors, can strain your inventory management and supply chain.
Building Resilience: Strategies for UK Retailers
While you can’t predict every disruption, you can take proactive steps to build a more resilient supply chain:
Diversify Your Supplier Base: Don’t rely too heavily on a single supplier or region. Having multiple sources for key products reduces your vulnerability if one supplier faces problems. Explore UK-based alternatives, where possible, to mitigate international shipping risks.
Map Your Supply Chain: Understand your entire supply chain, from raw materials to the end customer. Identify critical points and potential bottlenecks. This knowledge will help you pinpoint where risks are highest and where you need to focus your resilience efforts.
Stress Testing and Scenario Planning: Imagine different disruptive scenarios (e.g. a major port closure, a key supplier going out of business) and assess the potential impact on your business. Consider developing contingency plans for each scenario.
Increase Inventory Buffer (Strategically): While you don’t want to overstock, holding a slightly larger safety stock of critical items you know sell can help you weather short-term disruptions in supply or unexpected spikes in demand. Use data to determine appropriate buffer levels for different products.
Build Stronger Relationships with Key Partners: Foster open communication and collaboration with your suppliers, manufacturers and logistics providers. Understanding their challenges and working together can lead to more agile responses during disruptions.
Negotiate Flexible Contract Terms: Where possible, try to negotiate contract terms that offer some flexibility in delivery schedules, order quantities or payment terms, allowing you to adapt more easily to unforeseen circumstances.
Invest in Technology for Visibility and Communication: Implement systems that provide real-time visibility into your supply chain, allowing you to track shipments, monitor inventory levels, and identify potential issues early. Ensure you have robust communication channels with your partners.
Develop Alternative Logistics Plans: Identify backup transportation routes and carriers in case of disruptions to your primary logistics network. Consider using a mix of transport modes, where feasible.
Consider Local Sourcing: Where quality and cost allow, prioritise sourcing goods from within the UK. This can reduce reliance on international shipping and potentially shorten lead times, making your supply chain more agile.
Cybersecurity Measures: Implement robust cybersecurity measures to protect your own systems and ensure your partners have adequate security in place to prevent disruptions caused by cyberattacks.
Insurance and Financial Planning: Ensure you have adequate insurance coverage to mitigate potential financial losses from supply chain disruptions. Maintain healthy cash reserves to help you navigate unexpected costs.
Regularly Review and Update Your Risk Management Plan: The risk landscape is constantly evolving. Regularly review your risk management plan and update it to reflect new threats and changes in your supply chain.
Resilience for Both Bricks and Clicks
The strategies above are relevant for both physical and online retailers but there are some specific considerations:
- Physical Stores: Focus on ensuring a consistent flow of goods to your shelves. Consider local warehousing options or flexible delivery schedules to mitigate transport disruptions.
- Online Stores: Prioritise reliable fulfilment and delivery to customers. Diversifying your carrier network and having backup warehouse locations can be crucial. Clear communication with online customers about potential delays is also essential.
Conclusion
In today’s unpredictable world, a resilient supply chain is no longer a luxury but a necessity for UK retail businesses. By proactively identifying potential risks and implementing robust mitigation strategies, you can protect your operations, maintain customer satisfaction and ultimately thrive, even when faced with disruptions. Investing time and resources in building supply chain resilience is an investment in the long-term success and stability of your business, both on the high street and online. It’s also something that’s easy to put off but you’ll thank yourself if you tackle it now.